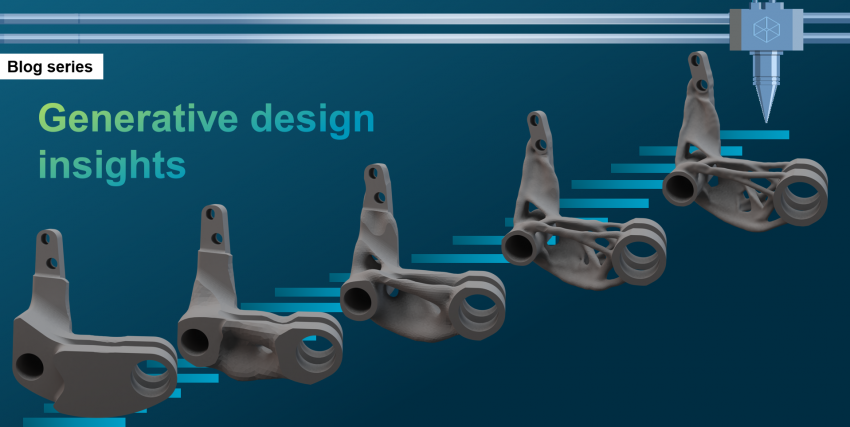
Our previous blog article “Generative Design Insights: Shifting the paradigm in 3D metal printing” dealt with the driving factors behind the emergence of generative design and what potentials arise for companies through the use of this technology. Analysts, therefore, expect significant market growth by the end of the decade. But what does Generative Design stand for, and what characterizes it?
Generative Design is characterized by a high degree of automation, flexibility, and overall high speed. The considerably increased computing power, which is also available in a scalable and flexible manner employing cloud computing, even without extensive hardware of one’s own, is the cornerstone of this development and the driver of progress in the entire simulation field.
The emerging trend towards Software as a Service (SAAS) further supports the application. Software is no longer purchased but also flexibly rented, depending on the user’s needs. In combination with artificial intelligence (AI) and machine learning (ML), even more diverse potentials will arise in the future in simulation, especially in generative design.
For component optimization, it is of particular interest to start with the broadest possible design space exploration to avoid limiting the solution by a too narrow starting range. What is crucial for the daily and successful use of the technology is a continuous process from start to finish. In particular, the underlying topology optimization was characterized by many steps and the need for different software solutions. This often leads to problems regarding data transfer and conversion, which frequently leads to a deterioration of the results and are time-consuming. That is where a key success factor of Generative Design lies: a continuous process that integrates all necessary steps.
This approach is a fundamental point of user-friendly Generative Design software designed for daily development processes. It must be straight and automated from the CAD import to the CAD export of optimized structures while maintaining high quality in terms of lightweight design, mechanical integrity and repeatability of the same results for the same tasks.
The basic process flow for Generative Design starts with the import of existing CAD data, if available. The geometry is then manipulated with the integrated geometry tools to create a complete optimization model. If no CAD data is available, the model can be built from scratch using the same tools. This includes the design space, non-design spaces such as contact surfaces, and constraints such as bearings and forces and moments. Further boundary conditions of the optimization are then defined, such as the stress value to be considered a key variable in the optimization, leading to a homogeneous stress distribution.
In the second step, the software then generates an optimization model including FE mesh fully automatically and in seconds and, based on the specified boundary conditions and target criteria, generates one or more fully usable, production-ready design candidates. Afterwards, the engineer evaluates the software results in the next step and, if necessary, further adjusts the requirements and target values. Once the user achieves a favourable outcome, the generated design can be analyzed and optimally prepared for production using a manufacturing simulation.
Stresses and deformations occurring during production are calculated and compensated for. Other sources of error, such as contact with the coater unit, can be analyzed and eliminated in advance. The software can also help find an optimal alignment and optimize the support structure. This manufacturing simulation prevents high costs that arise when errors occur during production. Especially in cost- and time-intensive additive manufacturing, this is recommended in any case. With completely simulated and optimized manufacturing, an error-free production can then directly start.
Another advantage of this combination of generative design and manufacturing simulation: CO2 emissions savings in various areas. Digital iterations in design discovery and manufacturing simulation eliminate the need for prototypes. Fewer failed attempts through trial-and-error not only save costs but are also more ecologically sustainable. That also applies to lightweight construction: Optimizing components with Generative Design results in weight-optimized lightweight designs. This, first and foremost, allows saving material in production. At the same time, it reduces production time in additive manufacturing because less material has to be melted in the manufacturing process. Less weight also means less energy consumption if the component is moved in use, for example, as part of a car or aircraft and in robotics or packaging machines. Overall, this results in savings in CO2 emissions in various areas and strengthens the company’s sustainability.

Engineers can create feasible, manufacturing-ready part designs easily with Generative Design. The optimization model is prepared based on the part’s requirements and simulated with an innovative algorithm utilizing sophisticated FEM. Then, the user can directly export the generated designs for validation or manufacturing preparation.
Leave A Reply